Filtration
Addfield, a trusted partner for over 35 years.
At Addfield we can provide a wide range of filtration systems suitable for various types of waste incineration systems.
Typically only required on ‘high capacity’ incineration plants but also installed onto smaller systems the Addfield Pollution Control Systems are capable of dealing with a range of emission parameters.
It is important to understand that any filtration system is only as good as the knowledge used to design and build it.
One solution will not fit all plants so serious consideration is required when taking into account chemicals, temperatures, flow rates, particulate sizes and the customers expectation.
That’s why at Addfield we work extremely closely with our clients to build a system that is right for their application, their waste stream and the resulting off-gas produced from it.
Quick Links
Click on the below links to view content.
Ceramic Filtration System with Acid Scrubber
The ceramic filter consists of a series of pollution control systems for specifically dealing with the off gas from an incinerator. Typically installed on a high capacity incinerator plant this pollution control system will capture all the gases, soot and entrained solids emitted to meet the European regulations, which are set out in directive 2000/76/EC. Such a filtration system typically has a high removal rate of 97% for particulates.
This dry filtration system operates by passing the exhaust gasses through a series of chambers and processes, these are:
The Heat Exchanger
A heat exchanger cools down gasses to between 400°C-420°C, this rapid temperature collapse from 1100°C help reduce dioxin and furan reformation. It also sets up the flue gas stream for the optimum temperature for the (following) acid scrubber function.
Acid Scrubber
Lime is fed into the system via a hopper, this material is then steadily injected into the gas stream, to neutralise the acidic gasses, such as HCL, HF and SO2. Spent lime is then removed by the final stage of the gas scrubbing process that is the particulates filtration system.
Ceramic Filtration System
Gas is pulled through vacuum formed ceramic filter tubes, these filters remove the heavy particulates and used lime in an extremely efficient manner. The gas is drawn through the system with a draught fan and the resulting clean, safe, gases are vented to atmosphere.
Cleaning System
Once the cycle is complete an automatic cleaning cycle can be initiated. This cycle reverse pulses compressed air through the ceramic filters, dislodging trapped particulates to clean them. Once complete the resulting material can be removed via the inspection hatch.
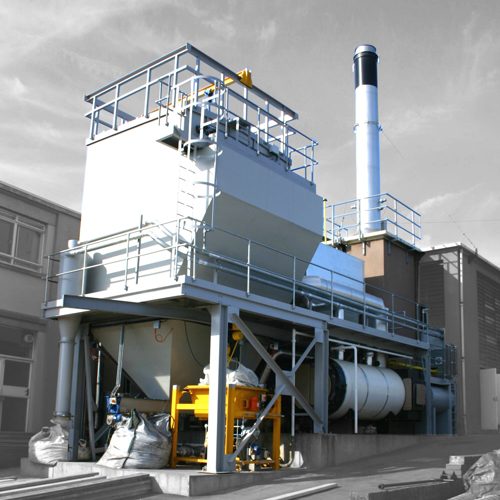
Advantages of a ceramic filtration system:
- Highest possible removal ratio (up to < 1mg/m3)
- Able to deal with multiple parameters removal
- Automatic cleaning system
- Heat recovery options
Venturi Filtration System
The Addfield wet scrubber system is primarily designed as particle suppressant system, ideally suited to high capacity incineration machines. Heavy particulates are removed from the exhaust gas using water injected from the roof of the scrubber system.
This bolt on system can be added to any incineration machine in the Addfield range and is scaled according to the specific application. Constructed from a stainless steel the vessel encapsulates multiple water spraying nozzles.
Incoming gasses are cooled prior to entering the scrubbing chamber. When incinerating waste containing halogenic compounds – often found in medical waste streams, an incinerator secondary after chamber will be operating at above 1100°C. This ensures thorough oxidations of flue gasses, dioxins and furans. When found in large quantities, dioxins reformation can occur at around 900°C. A sudden temperature crash will limit this reformation process. This sudden temperature drop happens prior to the gas stream entering the bottom of the scrubbing tower.
The gas stream will traverse upward, while liquid is sprayed downward into the incoming gas stream. This countercurrent flow exposes the outlet gas the lowest pollutant concentration to the freshest scrubbing liquid.
The smaller the droplets formed, the higher the collection efficiency achieved for both gaseous and particulate pollutants. However, the liquid droplets must be large enough to not be carried out of the scrubber by the scrubbed outlet gas stream as steam. Therefore, spray towers use nozzles to produce droplets that are usually 500–1000 μm in diameter. The gas velocity is kept low, from 0.3 to 1.2 m/s (1–4 ft/s) to prevent excess droplets from being carried out of the tower.
The primary function in which the wet scrubbers operate is to cause dust particles to attach to the water droplets. This contact occurs in three phases, these are:
Inertial Impact:
The direct impact of a particle with a water droplet, thus removing it from the emission gas stream. When the velocity between the two objects is relative this typically occurs.
Interception:
If a faster particle is not large enough to impact as water droplets, this gas particle may attempt to go around a slower or stationary object. As it does, its inertial energy will slow subsequently it is likely to impact a following water droplet in a scrubber system thus removing it from a the emission gas stream.
Diffusion:
Occurring in in particles typically less than .3 micron this process provides higher collection than would otherwise be expected due to the mixture of inertial impaction and Interception.
Acid Gas Removal
Calcium carbonate can also be added to water, with the resulting slurry sprayed into a flue gas scrubber. The process is found to be more efficient if a calcium hydroxide/water slurry is used, removing over 95% of Sulphur dioxide. The Sulphur dioxide is absorbed into the spray and precipitates as wet calcium sulphate. By re-circulating the slurry and injecting oxygen, calcium sulphate (gypsum) is formed which can be sold as a by-product. CaSO3 0.5H2O + 0.5O2 + 1.5H2O -> CaSO4 . 2H2O
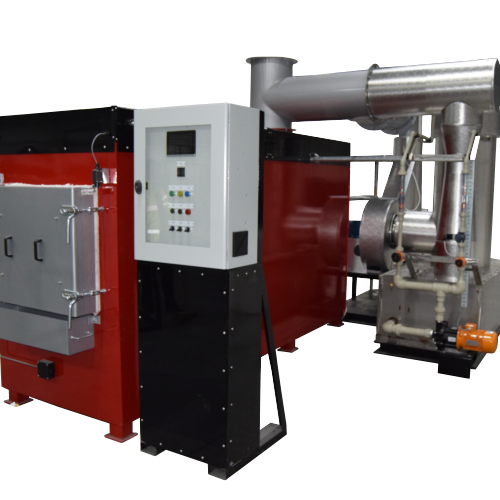
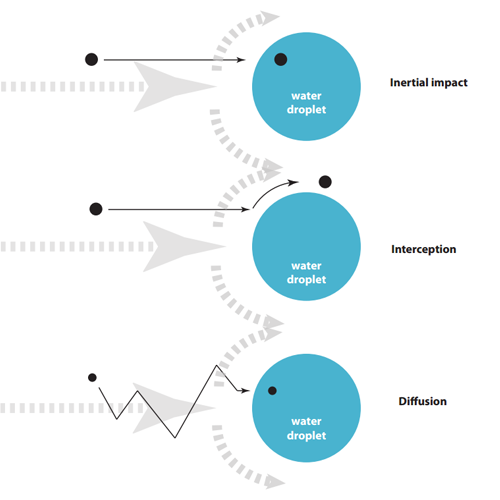
Advantages of a Venturi System:
Medium to high removal ratio
Capable of removing various parameters
Highly cost effective
What to know more? Find out how we used our wet scrubber systems in narcotics disposal case study.
Addfield Acid Scrubber System
Lime usage within incineration flue gas treatment is a proven technology. Acid gasses such as hydrogen chloride, (HCL), Sulphur dioxide (S02) and Hydrogen Fluoride (HF) can be treated with the Addfield Acid Gas Scrubber. These chemical compounds are commonly found in large numbers within the chemical and industrial industries and in smaller quantities in some chlorinated plastics such as PVC among other waste types.
Calcium hydroxide (hydrated lime) an alkali, is used to neutralise these acidic gasses. Lime is one of the most abundant and cost effective methods for tackling these chemical compounds. Feed rates are around 2kg/hr depending on the incinerator application.
Lime is fed into the resulting incineration gas stream via a hopper, this material is then steadily injected at a controlled rate, to neutralise the acidic gasses. Spent lime is removed by a secondary filtration system such as ceramic filter or cyclone system. The resulting spent lime is disposed at authorised landfill sites.
Acid scrubbers work most effectively at relatively low temperatures, around or below 410°C. Removal rates for dry scrubbing at these temperatures are approximately 90-99%.
High temperature acid scrubber is possible with removal rates of between 50-60% for sulfur dioxide. This is due to the porous nature of lime and its fast decomposition rates with in a high temperature environment
Powdered Activated Carbon
Powdered Activated Carbon (PAC) injection is widely used method to control heavy metals and dioxins emissions.
The porous structure of carbon makes it an ideal solution for absorption and it can be injected directly into the flue gas stream or laid in beds for the flue gas to pass through.
The injection temperatures, feed rate, material porosity and subsequent capture method determine the success rate of the material.
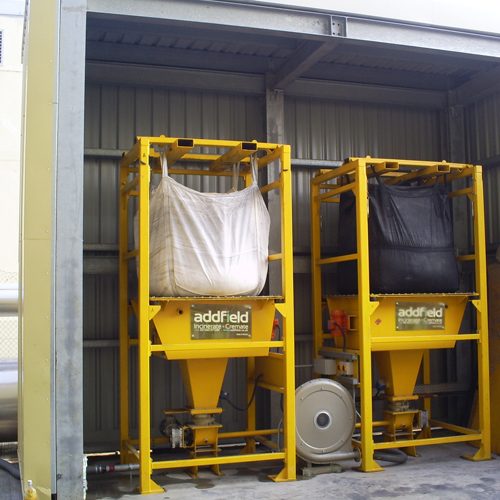
De-Nox Kits - Filtration Systems for Incineration Systems.
The Addfield De-NOx systems involves the use of Urea – a common, widely available harmless fertiliser to neutralise nitrogen oxides (NOx) formation.
NOx is widely problematic in coal plants and diesel vehicles and similarly more commonly found in high capacity diesel incineration plants.
Urea granules are dissolved in water and the resulting solution is injected directly into a separate chamber, post secondary after chamber combustion. The optimum flue gas temperature for injection is a 950°C, if the system operates at lower temperature or operates efficiency NOx emissions can actually increase. As such this chamber is temperature controlled and must remain in the window between 980°C and 830°C with a gas retention time not lower than 0.5 seconds.
This NOx removal process is known as selective not-catalytic reduction (SNCR). The process of nitrogen oxides removal using urea as a reagent in an aqueous solution (water and urea) injected into hot flue gases creates the post-combustion reactions:
NH2CONH2 + 2 NO + ½ O2 → 2 N2 + CO2 + 2 H2O
This system is an extremely cost effective way of controlling NOx with 1T of urea is typically costing between $220-$300USD (£140-£200) allowing for 620 hours of operation (Machine dependant).
Cyclone Scrubber Solutions
Cyclone scrubbers can be used as part of an incineration system as a dust particle removal system.
A cyclone scrubber must be specifically designed to meet the specific needs of the waste stream and the off gas produced to ensure optimum operation. A cyclone functions through a process called vortex separation, when the rotational effects and gravity are used to separate mixtures of solids from a gaseous emission stream.
The process requires high speed rotational air, typically derived from the incinerators combustion air system, however draft induced fans can be used to drag the gasses through the cyclone. Rotation of the gas is established directing the off-gas into a cylindrical container, subsequently the air flow forms a helix. As the air flow travels down the cylinder the heavier dust particles are forced to the edges of the helix because of the rotational forces. Heavier dust particles strike the cylinder walls they have too much inertia and fall to the bottom of the cylinder from where they are collected and removed.
The bottom of the cylinder is tapered to speed up air flow, increase the strike rate and to encourage a low pressure zone where the air flow will travel up and out of the cyclone once it has reached the base of the helix.
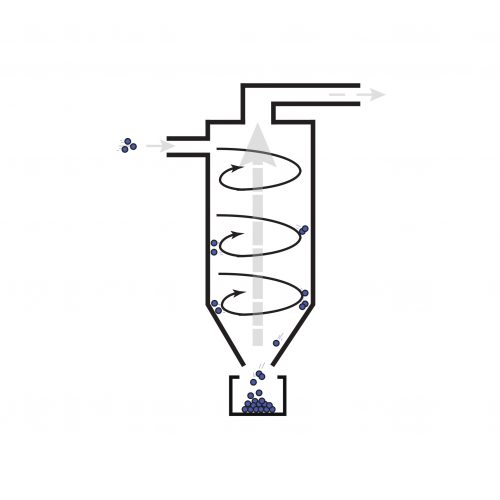
Advantages of a Cyclone:
- Medium particulate removal ratio
- No Moving Parts
- Cost effective