Client overview
Moredun Group is a worldwide renowned animal health and welfare centre, that specialises in the research into infectious diseases of farmed livestock.
In 1995, the government funded the installation of an incinerator to remove BSE, carcass and laboratory waste. The Science Park, home to Moredun Group, covers approximately 4 square miles. It takes a multifaceted approach to research, so a large and efficient incinerator is needed to keep up with the demand of the park and its changing needs. Back in 1995, a UK Government tender was won by Addfield – Techtrol. This was in-part due to the advanced technology used on similar sized sites, at other Veterinary Sciences Divisions around the country.
The importance of incineration
Incineration is vital for the destruction of clinical and animal waste, as it has potential to cause huge biosecurity issues if it is not contained on site and disposed of correctly. Equally, it was found to be a more cost-effective disposal method compared to alternative collection services offered.
The additional revenue it generated through heat recovery. Exhaust gases from the incinerator, are pushed through a double pass heat recovery boiler system. This system recovers steam and hot water in abundance. The steam is used to create humidity for specific environments, whereas the hot water is used for multiple applications across the large site.
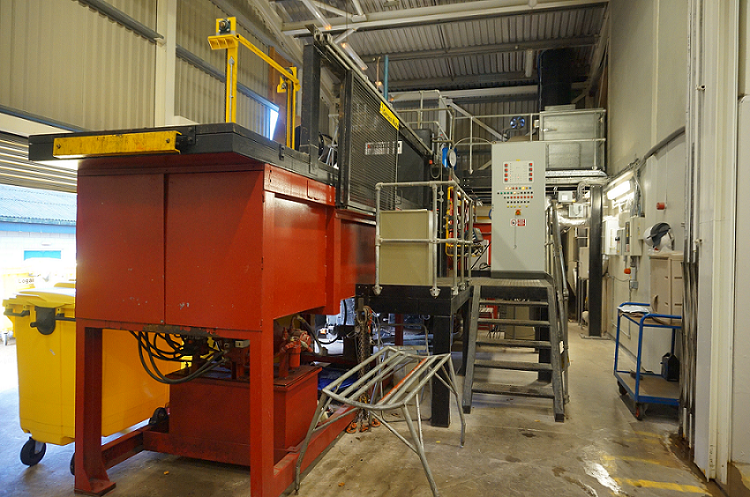
Which incinerator?
The AP200 machine was specified for this project. This system features an automatic waste charging system, consisting of a weigh plate to record incoming waste streams, 770L bin tipper system, waste charging ram and vertical lift doors inlet-vestibule doors.
Clinical waste is loaded via the wheeled bins, where as animals are loading by an electric overhead crane. Both systems have been designed to avoid or minimise the need for physical contact with the waste, whilst providing a process that is simple, reliable and effective to use.
The automatic loading system is complimented with an automatic de-ashing system. This de-ashing system will deposit ash in proprietary wheelie bin or FIBC Bag.
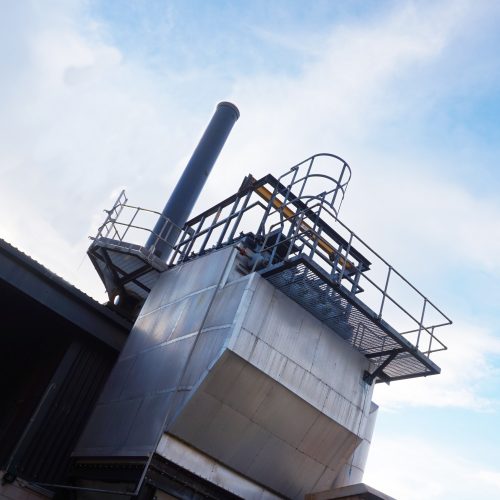
Long Term Operation
Between 2004 and 2006, the incinerator was upgraded to meet new legislation, WID (The Waste Incineration Directive EC2000/76). Additional filtration systems were added to the incineration plant to bring it in line with compliance. These included a dry ceramic filtration system and sorbet powder injection. Along with these upgrades, a WID compliant commissioning monitoring system was added. This system continuously measures its performance of the machine. It ensures conformance to the strict Environment Ministry Guidelines at all times.
The AP200 incineration machine is still in use today some 20+ years after installation and many thousands of cycles later. It is a testament to the design’s durability, robustness and efficiency.
Addfield ~ Simply built better.