The high value of reclaming waste
Sometimes it is not always clear how valuable waste can be. We all know the environmental value of recycling most materials, but may not be aware of just how much takes place on an industrial basis daily. New industries have formed to utilise the precious metals and materials in mobile phones, which contain various amounts of gold, silver and platinum. But what if the item itself consists of mainly Gold. Are systems in place to reduce loss during production and reclaim as much of these valuable resources?
One of the worlds leading watchmakers trusts Addfield to deliver the solution.
This was a question we faced recently when approached by one of the worlds leading manufacturers of luxury watches. Famous for using only high-quality 18-carat gold developed from their own foundries with many watches containing as much as 70 grammes of gold. As a manufacturer using only premium quality steel we are fully aware of the amounts of metal waste that can be produced just as a by-product of manufacturing but when that material can be worth over £50 per gramme well that’s when you need to really think seriously about your processes.
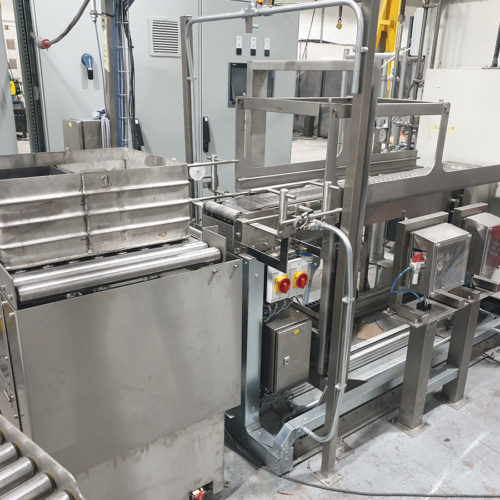
The most efficient solution for reclaiming Gold and precious metals.
This particular solution was more than 18 months in the planning and 12 months in production, installation and commissioning. Made all the more challenging due to the unfortunate situation with the Coronavirus heavily impacting upon our engineer’s ability to travel to Europe. A region with the highest number of luxury watch manufacturers anywhere and responsible for over half of the entire global production of luxury timepieces.
Our task as presented to us was to help them to develop a more efficient and modern approach to reclaiming a range of precious metals and materials from the production of their watches. Their existing system had reached the end of its effectiveness and was becoming in need of modernising. To keep up with current EU directives was essential as it was becoming more unpleasant to operate leaking fumes and simply becoming a less than ideal solution for such an important purpose. As we have found in many instances when a machine reaches the later years of its life it often becomes more cost-effective to replace than repair. In this case, the replacement would be able to bring with it many additional benefits and efficiencies and when you consider that each kilogram of waste processed through this machine could yield £2,000 worth of precious metal you can easily see the costs benefits to increasing efficiency.
A solution developed with the customer.
At Addfield we are committed to continuous research and development. Each and every time we build a machine we look at how we can make it better, more efficient, more environmental and better for the customer. Having this approach across our standard range we were more than ready to take on such a prestigious project. However, this was far from our traditional machine and we returned to the drawing board in almost every instance to provide the right solutions to each of our customers’ demands.
For a machine as complex as this required teamwork across all departments with key members of the design and production teams travelling out for site visits to gain a full understanding of the entire process that needed to be addressed, whilst ensuring that they could maximise the existing space. In addition to this, it ensured we were fully up to date with remote conferencing well before it became the new normal having almost weekly meetings with the customer to discuss developments, to install a machine to satisfy even the most demanding of needs.
This is how to reclaim precious metals through incineration
As legislation can change from year to year we ensured to go above and beyond the current regulations to ensure maximum conformity for many years into the future. The same approach went into developing the machine. Reviewing what worked and what didn’t about their previous systems we provided a machine that was built to last incorporating the following:
- A fully automatic operation.
- End to end tracking systems includes complete traceability between labs.
- Advanced operation consisting;
- automatic loading,
- processing,
- discharge,
- cool down,
- precious metal reclamation.
- Improved conformity with current Health and Safety guidelines through automation.
- Full abatement system.
- Thermal Recovery.
The entire operation has been designed to operate across two floors ensuring maximum user benefits.
Full transparency throughout design, construction and installation.
As this was such a unique project for both sides we welcomed the customers’ visits to the factory throughout the production of the machine. Alongside installing dedicated online webcams to enable them to connect and monitor the project remotely at any time. This was finished off with an extensive FAT (Factory Acceptance Test) being completed and passed before the system was taken apart and shipped to site.
A perfect example of the opportunities available through Addfield and our dedicated bespoke team at Addfield Projects, which specialises in the design, production installation and maintenance of one of a kind and specialised incinerators and high capacity solutions across all waste streams and industries.
The system has been in operation for some time now and the results have been as intended. delivering a more user-friendly operation that is efficient and delivering high-quality returns whilst being better for the environment and ensuring EU regulations are adhered to.
Although this project was the first of its kind we know it will not be the last as we are currently in the planning stages with multiple luxury goods manufacturers to begin commencement in the near future.