Dubai, UAE
MARS Inc has 2015 zero waste plan and 2 tonnes of waste which cannot be recycled. Being such a globally recognised company, they needed an alternative waste management method with a company they could trust to sustain its reputation of excellence. That’s where Addfield comes in.
The Importance of incineration
- Landfills are quickly reaching full capacity since the land has limited space.
- Buying an incinerator from a reputable company, such as Addfield, allows the possibility of waste-to-energy technologies being implemented.
- Pollution control is also a contemporary system which prevents incinerators from being the ‘smoking, smelling pollutants’ they have previously been known as.
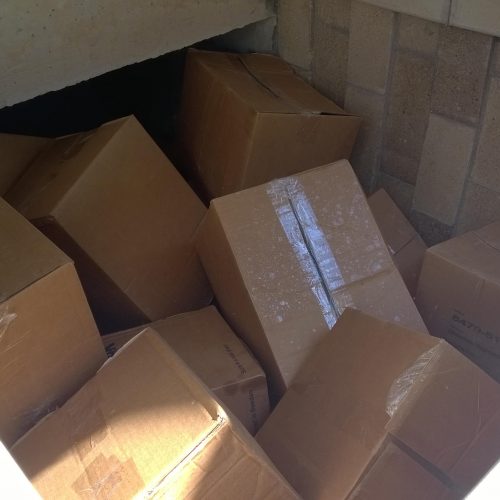
Fitting into the plan
A prototype machine was manufactured, and a program of emissions monitoring testing was performed at the Addfield manufacturing facility by a MCERT’s accredited, independent emission monitoring company. The results gained were used to measure its performance against stringent legislation.
The machine was delivered late in 2014 and has a load capacity of 1000kg. It was supplied with a high-temperature ash ejection vacuum system for ease of de-ashing.
Due to its success, the machine has been used as a pilot scheme, which has now been rolled out to other sites in Saudi Arabia.

Advantages of using Addfield incinerators
- Eco-cycle patented technology which means Addfield incinerators are the industry leaders in quality.
- Energy recovery options to further increase the environmental friendliness of Addfield machines.
- 30 years of experience in the industry. All ranges are built to the same industry-leading standard.
- Bespoke options available for true customer satisfaction
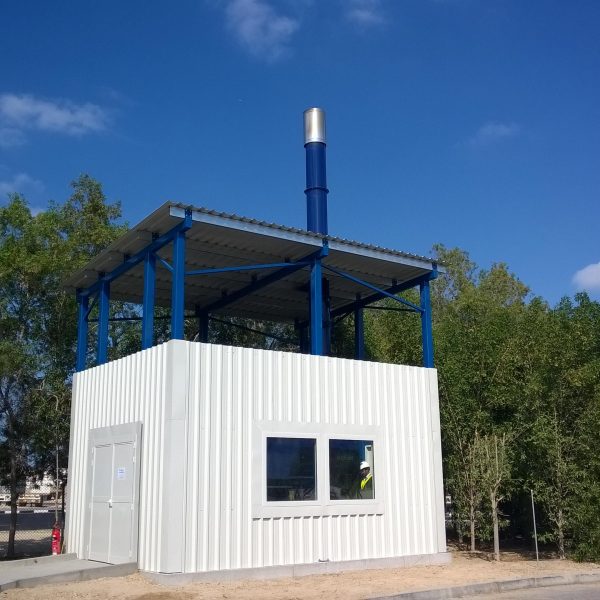
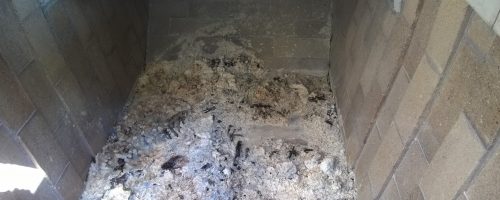
Which incinerator?
After an extensive research and development phase that focused on the specific types of waste generated on-site, including (but not exclusive to) food waste, packaging and laboratory waste, a bespoke machine was proposed and developed to deal with the waste generated.
The proposed bespoke machine had an: Increased after-chamber size, designed to deal with an increased emission flow rate and 1100C after-chamber temperature. PLC after chamber upgrade allowing for more control over a mixed waste stream Magnetic door interlocks to prevent unauthorised access.